- Manufacturer: Södra
- Designer: Claesson Koivisto Rune
- Material: DuraPulp
- Dimensions: 51 × 43 × 480 cm
- www.sodrapulplabs.com
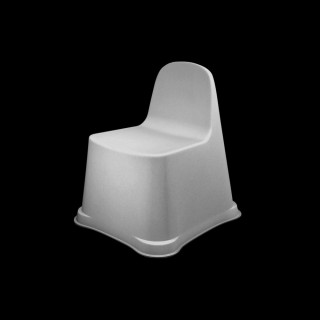
Index
- About The Parupu chair has been created by the Swedish architecture and design studio, Claesson Koivisto Rune and the Södra PulpLab research laboratory. Thi
- Manufacturer 'The world will be a better place with a little more paper' Paper is an organic material. It can be recycled time and time again. It's possible to m
- Material Durapulp : paper pulp and PLA The KTH Royal Institute of Technology and the companies STFI-packforsk and Södra have been collaborating since 2003 to c
- Criticism There are some serious problems with the use of corn to make packaging. First of all, corn is food. If the corn used to make PLA is animal feed, it sh
- Designers The architecture and design agency CLAESSON KOIVISTO RUNE was founded in Stockholm in 1995 by Märten Claesson, Eero Koivisto and Ola Rune. Their port
- Forestry Södra is one of the world's leading producers of market pulp. Most of the raw materials for our pulp come from forests owned by Södra's members who ar
- Production A tub is filled with pulp slurry. The chair mould is dipped into the tub. The chair goes into the oven to dry. The chair is hot-pressed to activate Du
- For Kids Why is making a chair from paper particularly suitable for children? As we all know, children grow fast which means they need furniture that is practi
- Other Chairs Enzo Mari's Seggiolina Pop for Magis is a kids' chair that ticks all the right boxes: great colour palette, so light the kids can move it themselves (
- Parupu Vadai Vadai is a traditional South Indian comfort food. [...] It is one universal food that you can never go wrong with, Parupu Vadai. Deep fried, crunchy l
The Parupu chair has been created by the Swedish architecture and design studio, Claesson Koivisto Rune and the Södra PulpLab research laboratory. This collaborative work, a new paper product, was demonstrated for the first time at Zona Tortona 2009 in Milan.
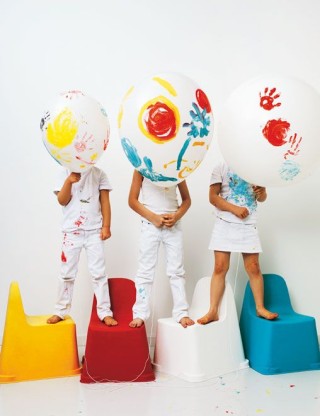
Mission
'It's time to change everything we know about paper,' is the mission statement of Södra Pulp Labs. And that's what the Swedish architecture firms that partner with the labs are doing as they wrap their minds around 50 years of research on pulp-based materials.
'Could it be durable? Waterproof? Light and insulating? Hard as Kevlar? We don't know the answers, but you're welcome to join us as we find them out,' says the lab.
Well, one thing is for sure: it can be kid-proof, such as the Parupu kids's chair. [...] Designed for the Milan Furniture Fair 2009, the chairs are stackable for extra play date seating and are seen as a great way to spare our forests and avoid petroleum-based plastics. Made of compostable Durapulp [...], they are sturdy like their name indicates and a way to keep the well-designed nursery free of that oh- so-yucky chemical smell that can take weeks to air out.
'The world will be a better place with a little more paper'
Paper is an organic material. It can be recycled time and time again. It's possible to make it very durable. But it can also be composted or combusted for energy recovery when you don't need it anymore. It doesn't harm the human body, not even if you use it internally. And it never releases more carbon dioxide into the atmosphere than what nature itself can take care of.
Paper is a cheap material. If we manufacture a separator from paper it costs less than the cleaning chemicals for a metal separator. That translates into something corporations understand – profit. But what would it mean for people in the third world if you could build functional houses for a fraction of today's cost? Or for disaster aid if a sleeping bag were to cost a dollar instead of fifty or a hundred?
Paper is a light material. Imagine if we could manufacture furniture that you could pick straight up when you wanted to vacuum underneath. Or crashworthy cars that you could carry into the garage when you got home from work. What would that mean for transportation around the globe? For costs and emissions and accidents? Quite a lot, we believe. That's why we will continue working in our lab.
Durapulp : paper pulp and PLA
The KTH Royal Institute of Technology and the companies STFI-packforsk and Södra have been collaborating since 2003 to create DuraPulp, which combines paper pulp and PLA (a biodegradable plastic) to create an incredibly resistant paper. Only two millimeters thick, DuraPulp can bear weight, tension, and humidity, as well as temperature changes.
This extremely clever invention benefits from the inherent qualities of paper: it's cheap, it's light, and it's organic. The fundamental fragility and short-life of paper are offset by the addition of plastic, which in turn makes DuraPulp an incredibly durable building material for furniture. The secret is in the recipe: mix paper pulp and polylactic acid together, then heat to precisely 167 degrees Celsius. The plastic encapsulates the paper fibers to create a material as strong as wood, steel or hard plastic! The most interesting aspect of this composite is that it challenges the usual boundaries of paper and reveals its unlimited potential as a green material, an unlikely yet successful innovation summed up by PulpLab's slogan: 'The world will be a better place with a little more paper.'
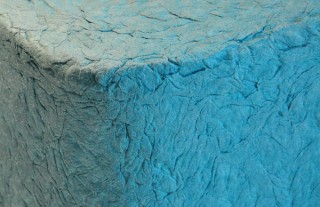
Bio-Plastic
Bio-plastic is a natural resin made from corn starch designed to supplement or even replace conventional petroleum based plastics. Years of research in the attempt to find natural alternatives has lead to the development of a process that converts corn starch successfully into a material which carries plastic characteristics. The bio-plastic is compostable and can completely return to nature after being used when buried. It will not degrade in salt water or sand.
PLA
For those of you still new to the whole corn-based plastics thing, the main component of this 'bio-plastic' is polylactic acid, also known as PLA, a resin that comes from the fermentation of the raw biomass from plants (like corn). PLA by itself is biodegradable, does not generate dioxin when burnt, or other harmful gases. […]
However, the PLA-based plastic can be processed after the end of use of the product and by doing so, the corn-based component can safely degrade.
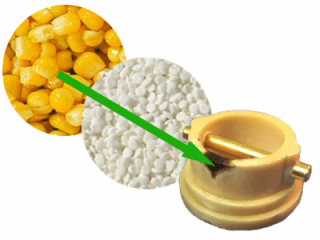
There are some serious problems with the use of corn to make packaging. First of all, corn is food. If the corn used to make PLA is animal feed, it should be used to feed animals to prevent the chronic protein deficiency experienced by people in developing countries. (The use of corn for ethanol has contributed to a price increase for this most basic of foods and also an increase in the price of soybeans, another basic food. Land originally used to plant soy was converted to corn in hopes of higher price for corn.) The 'steep environmental toll of industrially grown corn' [...] is a second reason not to promote PLA for packaging. [...] It takes a lot of water to grow corn. Water is our most precious resource and every continent (except Antarctica) is experiencing shortages - which will intensify as population increases.
The extensive use of the fertilizer used on this corn (nitrogen) is resulting in the pollution of aquifers in the midwest and the Gulf of Mexico. The Gulf of Mexico has a dead zone the size of New Jersey due to nitrogen used for corn for PLA and ethanol. [...] The farmers have switched over to the growing of this corn instead of feedstock corn and other crops like wheat. Food prices have gone up 10-13% according to the Dept. of Labor in one year, all attributed to less feedstock corn according to Lance Foods, Perdue and Smithfield Farms. Life cycle studies state that corn based PLA uses MORE fossil fuels than polyethylene. [...] The Environmental Defense Org. stated in Nov. 2007, that PLA is creating more global warming pollution than gasoline.
The architecture and design agency CLAESSON KOIVISTO RUNE was founded in Stockholm in 1995 by Märten Claesson, Eero Koivisto and Ola Rune.
Their portfolio contains buildings, interior designs, lighting solutions, furniture, textiles ect. Everything designed and created from quite a simple philosophy : to create, to improve and never to repeat!
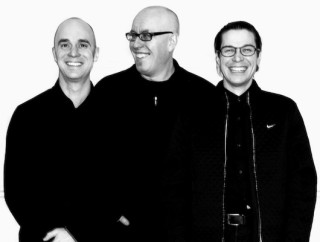
Joakim Nygren's master of science thesis - The author contacted designers Claesson Koivisto Rune arkitektkontor in august 2007 regarding his master thesis at KTH. [...] The company had discussed the possibility of creating a chair made from moulded pulp. [...] The objective was to produce design documentation for a paper pulp chair which was to be launched at the in 2008 Milan furniture fair. The purpose of the thesis was to develop a product with scientific methods as well as to investigate how to make collaboration between designers and engineers easier through communication.
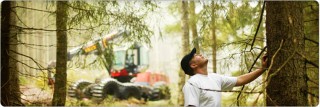
Södra is one of the world's leading producers of market pulp. Most of the raw materials for our pulp come from forests owned by Södra's members who are mainly small farmers in southern Sweden. Timber harvested from certified forests allows us to produce PEFC and FSC certified pulp.
Sweden
If half the world's forests were run like Sweden's, the entire greenhouse effect could be eliminated. [...] A radical overhaul of global forestry along Swedish lines would see carbon locked in a growing reserve of timber rather than remaining in the atmosphere in the form of carbon dioxide, which is responsible for the greenhouse effect.
Södra
More than 50,000 forest owners in southern Sweden are members of the economic association that is Södra. They own just over half of all privately owned forest in the area, as well as a group of companies that are successful in both Swedish and international markets. This gives them a market for their raw materials from the forest and at the same time provides the foundation for profitable forestry.
Södra is also a large employer. 3,700 people work for the Group, in areas that range from forestry management and environmental conservation to accounting, sales and product development. The Group's four business areas produce sawn and planed timber goods, interior products, paper pulp and biofuel. In recent years Södra has also become such a large producer of electricity that the Group now produces more electricity than it uses. Consideration for the environment is a natural element of our work even before the seeds are sown in the nursery.
Process
When you hold a newspaper, a sheet of paper or a package in your hand, it may have started out as a branch in one of the forests belonging to a Södra member. After being felled in the forest, pulpwood is transported by truck to Södra's pulp mills.
The wood raw material contains the cellulose fibres that become pulp. The production process is based on separating these cellulose fibres from by-products. The by-products are then taken care of in a number of other cycles, one of which is energy. Even chemicals are recycled. Production is highly automated and almost everything is controlled and managed by computers.
The pulp [...] is collected and burned to create heating energy, sometimes after having been pressed into pellets. The wood that is stripped of its bark is chopped into chips. To separate the cellulose fibres in the wood, the chips are cooked. The cellulose is then washed and bleached. When the last unwanted by-products have been removed from the pulp, it is dried and cut into appropriately-sized sheets that are strapped together into bales for transporting on to paper mills.
A tub is filled with pulp slurry.
The chair mould is dipped into the tub.
The chair goes into the oven to dry.
The chair is hot-pressed to activate DuraPulp.
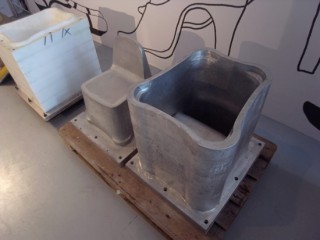
Why is making a chair from paper particularly suitable for children? As we all know, children grow fast which means they need furniture that is practical and well-designed yet doesn't cost a fortune. Besides, once it's outgrown or worn-out it is safely composted. An ecological sustainability benefit that counts a lot when making things for small people who belong to the future.
Life Cycle
This is a great example of holistic design; the project began with the intention of creating a fully recyclable cellulose based material, it evolved into the shape of a rounded, stackable and colourful chair that fits its intended use in kindergartens, and has been designed to the very last moments of the product life cycle. Parupu is a one piece object with no inserts that has been conceived to last the length of a childhood to later be recycled.
Indra Merca, designer of the BioSeat:
'I created a child's chair, because it was too complicated to create a chair for adults working in home conditions. The surface area for an adult chair is larger, therefore it needs extra ribbing. A child's chair can be made with the help of physically lighter and cheaper moulds. That was also the reason why I chose a child's chair.!'
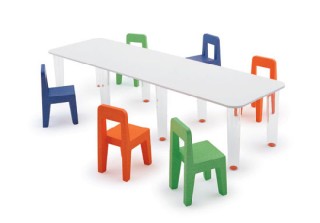
Enzo Mari's Seggiolina Pop for Magis is a kids' chair that ticks all the right boxes: great colour palette, so light the kids can move it themselves (or create houses and play structures), super sturdy and user-friendly. Plus it's stackable and biodegradable.
Made from sintered expanded polypropylene, the chairs are available in orange, blue or green.
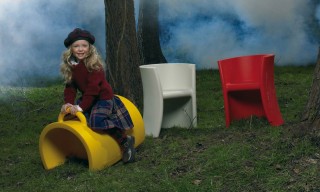
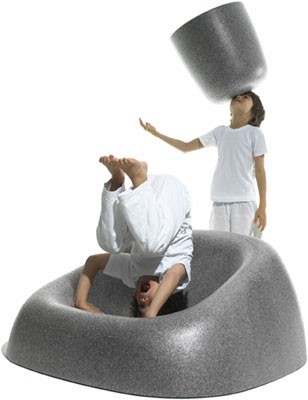
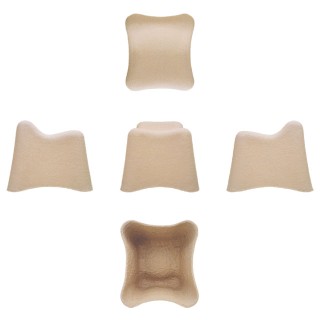
Chairs made from pressed recycled cardboard. Once no longer of use they are easily recycled again.
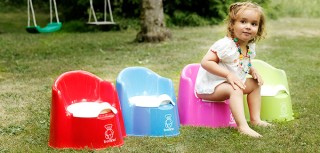
This chair looks just like a regular toilet (minus the flusher) and is funky enough to leave out when guests arrive. An ergonomically-designed seat makes long visits comfortable. And the arm rests allow kids to fully relax.
Clean up: Quick and painless. Simply lift out the bowl and wash.
Added bonus: A rubberized bottom keeps the seat secure.
Downfall: If your kid needs a bit of encouragement, this isn't the potty for him. There are no stickers, songs or lights to flash in acknowledgement of his success.
Vadai is a traditional South Indian comfort food. [...] It is one universal food that you can never go wrong with, Parupu Vadai. Deep fried, crunchy lentil fritters.
Making it is all about the consistency of the batter. It should [...] hold its shape in your hand. [...] To make, add the water a little bit at a time, until the lentils can be ground without turning into a mush. A few whole pieces of the lentils in the batter is fine.
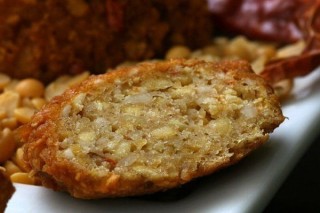