- Manufacturer: Kyocera Corporation
- Material: ceramic zirconium oxide blade
- Dimensions: 25 × 3 / 28 × 5 / 29 × 5
- www.kyocera.co.uk
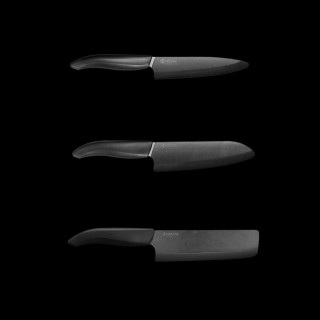
Index
- Material A ceramic knife is a knife made out of very hard ceramic, often zirconium oxide (ZrO2). These knives are generally produced by compacting Zirconia pow
- Advantages Advanced ceramic is second only to diamond in hardness. Long-wearing and corrosion-free, ceramic parts are often used in bone replacement procedures.
- Demonstration
- Applications Advanced ceramics, such as Alumina, Silicon Nitride and Aluminum Nitride are currently being used to manufacture critical aerospace components, becaus
- Security Ceramic knives present a conceptual problem to the security industry since ceramics are not picked up by metal detectors. To solve this problem, many
A ceramic knife is a knife made out of very hard ceramic, often zirconium oxide (ZrO2). These knives are generally produced by compacting Zirconia powder using high pressure presses which apply a pressure of around 300 tons to produce blade shaped blanks. These blanks are very brittle and fragile which can be shattered by a slight blow and special binders are used to retain the shape of the blank until the firing process. Like all ceramics these are consolidated into a dense and strong ceramic by solid state sintering at approximately 1400 degrees centigrade for 5–12 hours in a high temperature furnace. The result is a very hard and blunt blade which needs to be sharpened to get the desired cutting edge. The blades are sharpened by grinding the edges with a diamond dust coated grinding wheel. […]
Several brands offer a black blade made by an extra firing or sintering via hot isostatic pressing (HIP). This process improves the toughness of the blade, the key limitation to using ceramics in knife blades.
Advanced ceramic is second only to diamond in hardness. Long-wearing and corrosion-free, ceramic parts are often used in bone replacement procedures.
In fact, ceramic components are used in satellites, racecar brake pads and other applications that require extreme wear-resistance. For those components that would virtually disintegrate if made from metal, ceramic is the material of choice.

Advanced ceramics, such as Alumina, Silicon Nitride and Aluminum Nitride are currently being used to manufacture critical aerospace components, because they have several advantageous physical properties. These inorganic, non-metallic materials retain dimensional stability through a range of high temperatures and exhibit very high mechanical strength. They also demonstrate excellent chemical resistance and stiffness-to-weight ratio, thereby providing manufacturers with the ability to design components that offer optimal performance in their intended application.
Electro-Ceramics
The 20th century brought the advent of electronics, with the start of radio and television broadcasts and the invention of the transistor. This era was facilitated by ceramics from the beginning, when large vacuum tubes of the early 20th century relied on ceramic materials. Within wireless equipment, only ceramics possessed the properties necessary to provide high signal output even over high frequency ranges. Ceramics could not be replaced with other materials. [...]
In addition, ceramics have helped to reduce the size of capacitors and inductors in electronics. Since the middle of the 20th century, ceramics have undergone a continual evolution, and now possess excellent dieletric and magnetic properties. As a result, electronic components were miniaturized and made highly functional. Ceramics thus made a significant contribution to the downsizing of electronic equipment. If capacitors had not been made of ceramics, the portable electronic devices we depend on every day, such as pocket-sized mobile phones and laptop computers, would never have appeared. In fact, a modern mobile phone uses more than 200 ceramic capacitors. Fine Ceramics were born in this era as highly precise industrial materials made through tightly controlled processes from refined or synthetic raw powders, thus differentiating them from all conventionally fired products.
Automotive Industry
The automotive industry has developed substantially through advances in mechanical technologies, and technologies such as electronics and advanced materials have also contributed to further advances in automobiles. The contribution of ceramic materials to automobile technologies ranges over driving performance, exhaust gas purification, and fuel efficiency improvements. Several ceramic components, such as knock sensors, oxygen sensors, exhaust gas catalysts, and silicon nitride parts for automotive engines, have been successfully applied to automobiles. This paper focuses on the contribution of ceramics to automotive technologies. It also mentions potential contributions in the future, including adiabatic turbo-compound diesels, ceramic gas turbines, fuel cells, and electric vehicles because ceramic technologies have been intensively involved in the challenge to achieve advanced power sources.
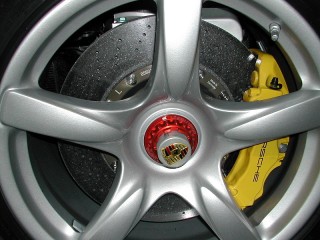
Military
Ceramics such as alumina, boron carbide and silicon carbide have been used in bulletproof vests to repel large-caliber rifle fire. Such plates are known commonly as small-arms protective inserts (SAPI). Similar material is used to protect cockpits of some military airplanes, because of the low weight of the material. […]
Work is being done in developing ceramic parts for gas turbine engines. Currently, even blades made of advanced metal alloys used in the engines' hot section require cooling and careful limiting of operating temperatures. Turbine engines made with ceramics could operate more efficiently, giving aircraft greater range and payload for a set amount of fuel.
Medicine
Ceramic components have a reputation for handling the heat that would melt steel, and for being relatively easy to form if precision is not critical. But a recent family of ceramics is said to add to those features high purity, durability, and precision manufacturing that can produce components with clearances (between piston and cylinders) as tight as 0.000075 in. […]
Many of the ceramics are said to work well in electro-surgical devices because of their high strength, stiffness, and dielectric strength. And in other applications, low friction and long-wear characteristics let them work longer than metal versions would.
An advantage of ceramics over traditional metallic components and polymers, says the company, is that its recent ceramics have greater thermal stability, strength, hardness, and insulating capabilities. The firm adds that the material characteristics can be adjusted to particular tasks.
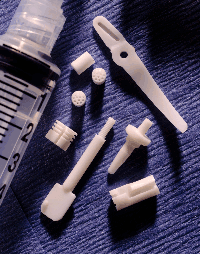
Bio-ceramics
Recently, there have been advances in ceramics which include bio-ceramics, such as dental implants and synthetic bones. Hydroxyapatite, the natural mineral component of bone, has been made synthetically from a number of biological and chemical sources and can be formed into ceramic materials. Orthopedic implants made from these materials bond readily to bone and other tissues in the body without rejection or inflammatory reactions. Because of this, they are of great interest for gene delivery and tissue engineering scaffolds. Most hydroxy apatite ceramics are very porous and lack mechanical strength and are used to coat metal orthopedic devices to aid in forming a bond to bone or as bone fillers. They are also used as fillers for orthopedic plastic screws to aid in reducing the inflammation and increase absorption of these plastic materials. Work is being done to make strong, fully dense nano crystalline hydroxyapatite ceramic materials for orthopedic weight bearing devices, replacing foreign metal and plastic orthopedic materials with a synthetic, but naturally occurring, bone mineral. Ultimately these ceramic materials may be used as bone replacements or with the incorporation of protein collagens, synthetic bones.
Ceramic Needles
New polymerization technology may one day take the pain out of injections and blood draws.
A team of researchers at the University of North Carolina and Laser Zentrum Hannover have recently used two-photon polymerization to create hollow needles so fine patients wouldn't feel them piercing their skin. Clustered together on a patch, these microneedles can deliver drugs or draw blood efficiently as standard hypodermic needles. These findings are reported in the International Journal of Applied Ceramic Technology.
Developing a way to deliver drugs intravenously with minimal pain and trauma, by someone without medical expertise, has long been a mission of biomedical engineers. Until recently, their most promising product had been stainless steel and titanium microneedles. These metal microneedles, though, are prone to break on impact with skin.
Ceramic knives present a conceptual problem to the security industry since ceramics are not picked up by metal detectors. To solve this problem, many manufacturers of non-military knives include a quantity of metal in each knife to ensure they are detectable with standard equipment. Ceramic knives can be detected by extremely high frequency scanners (e.g. millimeter wave scanners), although (as of 2006) these scanners are not yet in widespread use.