- Manufacturer: Magis
- Designer: Jasper Morrison
- Material: reinforced polypropylene
- Dimension: 78 × 49 × 51 cm
- www.magisdesign.com
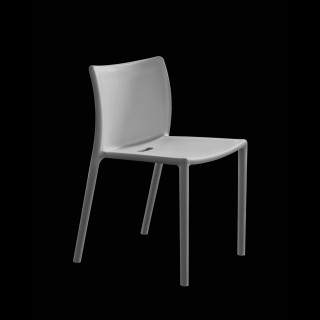
Index
- Technology Supremely practical, the stacking chair has fascinated modernist designers for decades. The British designer Jasper Morrison (1959-) began work on his
- Manufacture Injection moulding is a manufacturing process for producing parts from both thermoplastic and thermosetting plastic materials. Material is fed into a
- Typology Jasper Morrison's Air Family continues to expand with the addition of the folding Air Chairs and Low Air Table & Air TV Tables. The original Air Chair
- Designer [Jasper Morrison] cites his early inspirations as his grandfather's study - a light, bright room furnished in the modernist style and an Eileen Gray e
- A White Chair What's the world's most famous chair? […] It's neither an icon from the design history books, nor a symbol of political power, but one of the cheap pl
Supremely practical, the stacking chair has fascinated modernist designers for decades. The British designer Jasper Morrison (1959-) began work on his stackable Air-Chair when Eugenio Perazza, the owner of Magis in Italy, showed him a length of tube made by gas injection, a new plastic moulding technology. 'The design began from the leg up, describing the tubular structure of a chair to which a thin skin is applied for the seat and back, in much the same way as the earlier Plywood Chair uses a thicker plywood for the structure and a thinner plywood for the seat,' recalled Morrison. 'I think we succeeded in delivering a combination of angles and curves which give a lot of comfort.'
Functionality
Back in 2000, Jasper Morrison's Air Chair for Magis changed the face of outdoor living areas. Suddenly, here was a durable, innovatively light chair. You could stack it and, best of all, the colour didn't fade in the sun.
Brynn Blumberg […] sums up why the Air Chair has made plastic such a material for our times. 'It works for indoors and outdoors, it's inexpensive, it's sustainable and it's really multifunctional,' he says. 'A common thing I am hearing young people say is that they are buying a set of chairs to initially use around their dining table, then in a couple of years they will move them outside.' And it's cheap. 'They're made to last and they aren't ridiculously expensive. You can afford a designer piece [of plastic furniture] without taking out a second mortgage,' he says. Plastic is an affordable entry point into genuine designer furnishings so it has status value.
Injection moulding is a manufacturing process for producing parts from both thermoplastic and thermosetting plastic materials. Material is fed into a heated barrel, mixed, and forced into a mould cavity where it cools and hardens to the configuration of the mould cavity. After a product is designed, usually by an industrial designer or an engineer, moulds are made by a mouldmaker (or toolmaker) from metal, usually either steel or aluminium, and precision-machined to form the features of the desired part.
Injection moulding is used to create many things such as milk cartons, packaging, bottle caps, automotive dashboards, pocket combs, and most other plastic products available today. Injection moulding is the most common method of part manufacturing. It is ideal for producing high volumes of the same object. Some advantages of injection moulding are high production rates, repeatable high tolerances, the ability to use a wide range of materials, low labour cost, minimal scrap losses, and little need to finish parts after moulding. Some disadvantages of this process are expensive equipment investment, potentially high running costs, and the need to design mouldable parts.
Gas Assisted Injection Moulding
Gas assisted moulding (GAM) is a relatively new technology in plastics injection moulding that offers opportunities to reduce moulding costs, improve quality and allows designers to be even more imaginative in the creation of injection moulded components.
Gas assisted moulding involves the introduction of nitrogen under pressure to the mould cavity at a set time during the moulding cycle. The aim is to either hollow out thick section mouldings or eliminate sinkage and/or warpage in thin section injection mouldings. Gas injection can also result in stronger parts due to the 'box section' effect. Variable thickness sections can be included. Hollow sections can be moulded without the need for mechanical cores. Rigidity can be achieved through hollow box sections. Several components may be combined on a single part. Inclusion of strengthening ribs, bosses and other features can be included without impairing surface appearance.
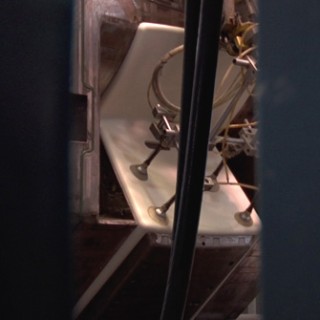
Parkesine and Celluloid
The first man-made plastic was invented in Britain in 1851 by Alexander Parkes. He publicly demonstrated it at the 1862 International Exhibition in London, calling the material he produced 'Parkesine.' Derived from cellulose, Parkesine could be heated, moulded, and retain its shape when cooled. It was, however, expensive to produce, prone to cracking, and highly flammable.
In 1868, American inventor John Wesley Hyatt developed a plastic material he named Celluloid, improving on Parkes' invention so that it could be processed into finished form. Together with his brother Isaiah, Hyatt patented the first injection moulding machine in 1872. This machine was relatively simple compared to machines in use today. It worked like a large hypodermic needle, using a plunger to inject plastic through a heated cylinder into a mould. The industry progressed slowly over the years, producing products such as collar stays, buttons, and hair combs.
The industry expanded rapidly in the 1940s because World War II created a huge demand for inexpensive, mass-produced products. In 1946, American inventor James Watson Hendry built the first screw injection machine, which allowed much more precise control over the speed of injection and the quality of articles produced. This machine also allowed material to be mixed before injection, so that coloured or recycled plastic could be added to virgin material and mixed thoroughly before being injected. Today screw injection machines account for the vast majority of all injection machines. In the 1970s, Hendry went on to develop the first gas-assisted injection moulding process, which permitted the production of complex, hollow articles that cooled quickly. This greatly improved design flexibility as well as the strength and finish of manufactured parts while reducing production time, cost, weight and waste.
Jasper Morrison's Air Family continues to expand with the addition of the folding Air Chairs and Low Air Table & Air TV Tables. The original Air Chair & Air Tables are increasingly popular as versatile, modern, lightweight solutions for both indoor & outdoor seating solutions.
Jasper Morrison (1959-) conceived the idea of the Folding Air-Chair when sitting on an old-fashioned wooden folding chair at a local residents' meeting. 'At the end the chairs were folded up so quickly and stacked into such a small space that I finally understood the benefits.' He devised the chair – an addition to the gas injected moulded polypropylene Air furniture he had developed for Magis since 1999 – to be 'assembled in seconds' from three pieces of moulded polypropylene connected with pivoting pins. Morrison believes that the application of advanced plastic moulding technology 'brings new life to a tired typology' making it suitable for use when a wooden or metal folding chair might seem incongruous.
[Jasper Morrison] cites his early inspirations as his grandfather's study - a light, bright room furnished in the modernist style and an Eileen Gray exhibition he saw at London's Victoria & Albert Museum. During his student years, Morrison became interested in the work of modernist pioneers - such as Buckminster Fuller, Gerald Summers, Jean Prouvé and Le Corbusier.
Even as an impecunious young designer, Morrison was determined to design for industrial production. Rather than making pieces by hand as many young designers do, he scoured London on his Honda 90 moped looking for small industrial workshops which would make up small quantities of objects from ready-made industrial components.
[Morrison's] modesty permeates his work. Unlike the overwrought styling of many of his contemporaries, the objects Morrison has designed appear at first sight almost not to have been designed at all: pared-down, essential, simple, yet always displaying something - a particular radius on a corner, perhaps, or a slight taper on a table leg - that discreetly reveals the care that has gone into them.
'I think a lot of what we do is reprocessing,' he says, meaning that he tries to adapt and improve on existing objects, rather than attempting to reinvent the wheel with every job. 'When you're young you're just designing stuff, but 15 years on you're just repeating typologies. You realise there's no point in doing it again unless it's going to be better than it was.' When asked to design a new dining chair, for example, he'll seek out what he considers to be the most perfect existing chair and see if he can reduce the weight a little, or make it a bit more comfortable.
What's the world's most famous chair? […]
It's neither an icon from the design history books, nor a symbol of political power, but one of the cheap plastic chairs that you can buy for a few euros, and spot just about everywhere, usually in white. Like most truly ubiquitous objects, they're so familiar that we barely notice them, but more people all over the world have seen — and sat on — one of those chairs, than any other. […]
Just think about how many there are in schools, bars, hospitals, parks, beaches, sports stadiums and retirement homes. And how often they appear as props in global dramas. Floating in the debris of the tsunami and Hurricane Katrina. Seating thousands of people at Cuban political rallies. Lurking in the hideout where Saddam Hussein was captured, and in Abu Ghraib prison. […]
The plastic chair even has a celebratory Web site - www.functionalfate.org - which is visited by over 30,000 people every month. It refers to the chair by its technical name, the monobloc, and invites visitors to submit photographs of them.
As a universally accessible, mass-manufactured object, the cheap plastic chair is a modernist ideal, but it's also something of an environmentalist nightmare. There are far more damaging plastics than polypropylene, but it isn't biodegradable and broken monoblocs are almost impossible to repair. Landfill sites are already stuffed with them, and millions more are on their way.
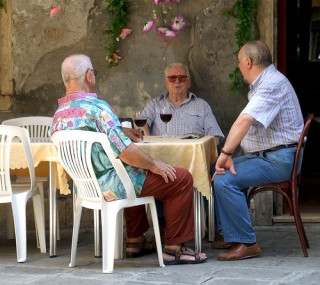
- www.nytimes.com/2007/02/04/style/04iht-design5.html?pagewanted=2
- www.flickr.com/photos/artcriminal/3959816963/in/pool-those-white-plastic-chairs
A History of Monobloc Plastic Chairs
The first all-plastic chair was designed by the Italian designer Joe Colombo in 1965. It was made in 5 pieces - the backrest /seat monococque and 4 single legs.
In 1967 the first monobloc chair was invented. 'Selene' by the Italian Designer Vico Magistretti, made from just a single piece of 3 mm thick reglar (fibreglass-reinforced polyester). [...] At the same time, another structural one-piece plastic chair was developed by Danish designer Verner Panton. It was a cantilever chair (with no rear legs) made of Luran S plastic (acrylate-styrene-acrylonitrile) and could be produced only in 1970s with the development of injection-moulding technology.
The very first mass-produced monoblocs probably came from the French Allibert Group or the US Grossfillex Group.
Millions have been produced since their debut in the early 1980s. Every seventy seconds a monobloc chair comes out from a single press. 220°c hot polypropylene is mashed through the extruder into a mould. There are only fractions of a millimetre slack between the two halfs of the mould that endure a pressure of 1,000 tons.
Early anonymous monoblocs cost around $60 each, but as more and more were manufactured, the price dropped to less than $3. They are manufactured in Russia, Taiwan, Australia, Mexico, United States, Italy, France, Germany, Morocco, Turkey, Israel and China, among other countries.
Monoblocs are a universally accessible, mass-manufactured object, landfill sites are stuffed with them, and millions more are on their way.