- Manufacturer: 3M
- Designer: Ergonomidesign
- Material: polycarbonate, LCD glass
- Dimensions: 22 × 28 × 30 cm
- www.3m.com
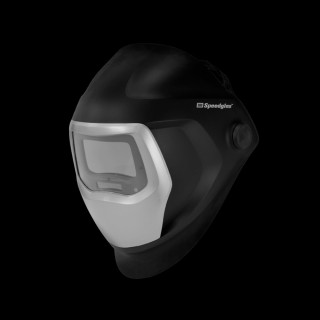
Index
- Welding Mask Definition Welding helmets are headgear used when performing certain types of welding to protect the eyes, face and neck from flash burn, ultraviolet light, spar
- Auto Darkening Auto darkening welding helmets offer an intuitive protection to modern welders. These helmets automatically darken when a welder strikes the arc. They
- Materials Polycarbonates Polycarbonates are a particular group of thermoplastic polymers. They are easily worked, moulded, and thermoformed; as such, these plas
- Welding GTAW/ TIG welding Gas tungsten arc welding (GTAW), also known as tungsten inert gas (TIG) welding, is an arc welding process that uses a nonconsumable
- History During the 1920s, major advances were made in welding technology, including the 1920 introduction of automatic welding in which electrode wire was con
- Dangers Welding accidents It's one of the most regulated areas of the construction industry, but it's also one of the most dangerous. Welding accidents injure
- Extreme Welding Hyperbaric welding Hyperbaric welding is the process of welding at elevated pressures, normally underwater. Hyperbaric welding can either take place w
Welding helmets are headgear used when performing certain types of welding to protect the eyes, face and neck from flash burn, ultraviolet light, sparks and heat. Most commonly used with arc welding processes such as shielded metal arc welding, gas tungsten arc welding, and gas metal arc welding. Welding helmets are necessary to prevent arc eye, a painful condition where the cornea is inflamed. Welding helmets can also prevent retina burns, which can lead to a loss of vision. Both conditions are caused by unprotected exposure to the highly-concentrated UV rays emitted by the welding arc (which can also damage uncovered skin, similar to a sunburn).
All welding helmets include a small window, called a lens shade, through which the welder looks at the weld. In older helmets, the window can be made of darkly tinted glass, or perhaps a pair of polarized lenses. In more modern helmet designs, transparent material that darkens automatically when exposed to the flare of a welding arc are more common. Either type, however, is susceptible to damages such as cracks that can compromise the protection from ultraviolet rays. In addition to the lens shade, the helmet has a shroud around the face to protect it from hot metal sparks generated by the arc. Some older models have a leather covering protecting the neck and shoulders as well.
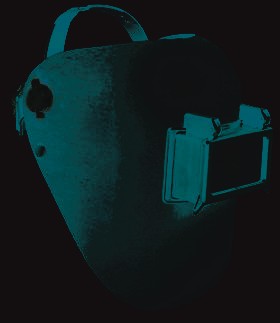
Auto darkening welding helmets offer an intuitive protection to modern welders. These helmets automatically darken when a welder strikes the arc. They free the hands that in the past had to lift and lower the faceplate, or remove the helmet altogether to see. Many injuries have been eliminated by auto darkening helmets because they cover a welder's eyes at all times without risking exposure to irritating fumes and flying debris. By instantly responding to light, these helmets auto darken when the welder strikes the arc and clear up after the welder shuts off the arc.
Auto darkening welding helmets prove especially useful to welders working indoors under poor light conditions. Traditional welding helmets can literally blind a welder if he has to suddenly cease welding and kill the arc, leaving himself in total darkness and subject to fall and/or injury. Because of this, many construction companies now require all of their welders to use auto darkening welding helmets so they can see to walk the buildings they are working in. Auto-darkening helmets also help farmers working outside because they react to sunlight much like the light of an arc. In future years, it is very likely all welding helmets will be auto darkening not only because they are more convenient than standard helmets, but also because their ever-increasing precision allows for customized eye protection - something Federal authorities and Insurance agencies may soon require.
There are two types of auto darkening helmets that welders use. One is battery powered; the other is solar powered. Solar power is more convenient and efficient when working outside, but work deep inside of large structures, or even underground, will require battery-powered helmets. Both employ sensors to 'know' when the light brightens, and when it is time to adjust the special glass in the face shield to block just the right amount of light. From time to time a welder calls in with the question, 'Won't the arc from my fellow welder trigger the auto darkening glass?' The answer could be yes or no, depending on the model in question. Basic models will grow darker with any exposure to arc light, regardless of the source. Deluxe auto darkening helmets have a sensor built into their design that 'understands' the difference between the operator's arc and a coworker's arc. For private individuals working by themselves, it makes little difference, if any, if the helmet has an auto-darkening sensor like this. For a company, however, it is best to invest in hightened auto darkening welding helmets to have a sensor for secondary arc light. It simply makes sense to do so.
3M Speedglas 9100
The 9100 is the ideal shield for the professional welder – a shield with optimised protection, comfort, and performance. The revolutionary design fundamentally changes how the welder wears the shield, giving the user the most comfortable fit available with perfect balance.
The 9100 is the result of welder comment from all around the globe and is the new product benchmark for the entire market of premium personal protective equipment for welders.
The new 9100 series features three models that are differentiated by size: the Speedglas 9100V, 9100X and 9100XX have normal, large and extra-large viewing areas, respectively.
Polycarbonates
Polycarbonates are a particular group of thermoplastic polymers. They are easily worked, moulded, and thermoformed; as such, these plastics are very widely used in the modern chemical industry. Their interesting features (temperature resistance, impact resistance and optical properties) position them between commodity plastics and engineering plastics. Their plastic identification code is 7.
Polycarbonate is becoming more common in housewares as well as laboratories and in industry, especially in applications where any of its main features—high impact resistance, temperature resistance, optical properties—are required.
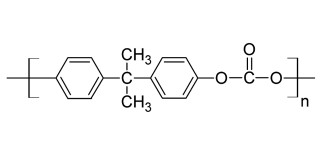
LCD
Liquid crystals find wide use in liquid crystal displays, which rely on the optical properties of certain liquid crystalline substances in the presence or absence of an electric field. In a typical device, a liquid crystal layer (typically 10 μm thick) sits between two polarizers that are crossed (oriented at 90° to one another). The liquid crystal alignment is chosen so that its relaxed phase is a twisted one [...] This twisted phase reorients light that has passed through the first polarizer, allowing its transmission through the second polarizer (and reflected back to the observer if a reflector is provided). The device thus appears transparent. When an electric field is applied to the LC layer, the long molecular axes tend to align parallel to the electric field thus gradually untwisting in the center of the liquid crystal layer. In this state, the LC molecules do not reorient light, so the light polarized at the first polarizer is absorbed at the second polarizer, and the device loses transparency with increasing voltage. In this way, the electric field can be used to make a pixel switch between transparent or opaque on command. Color LCD systems use the same technique, with colour filters used to generate red, green, and blue pixels. Similar principles can be used to make other liquid crystal based optical devices.
Thermotropic chiral LCs whose pitch varies strongly with temperature can be used as crude thermometers, since the colour of the material will change as the pitch is changed. Liquid crystal colour transitions are used on many aquarium and pool thermometers. Other liquid crystal materials change colour when stretched or stressed. Thus, liquid crystal sheets are often used in industry to look for hot spots, map heat flow, measure stress distribution patterns, and so on. Liquid crystal in fluid form is used to detect electrically generated hot spots for failure analysis in the semiconductor industry. Liquid crystal memory units with extensive capacity were used in Space Shuttle navigation equipment.
It is also worth noting that many common fluids are in fact liquid crystals. Soap, for instance, is a liquid crystal, and forms a variety of LC phases depending on its concentration in water.
Priva-Lite Saint Gobain
Glazing with ordered opacification, product type SGG PRIVA-LITE® from Saint-Gobain Glass, changing from non-transparent to transparent by the application of an electric voltage of approximately 100 V AC.
SGG PRIVA-LITE® is a laminated glass panel made of 2 extra clear glasses and a liquid crystal interlayer film (LC Film). The film is sandwiched between two interlayer films and assembled between the glass panes. The components are laminated together to form a compact assembly.
When switched OFF, the liquid crystals are randomly positioned, giving the glass a translucent, milky white appearance, and preventing through vision. When switched ON, the liquid crystals orientate themselves in the same direction; the glass becomes transparent and allows vision through it. Switching between ON and OFF states is almost immediate.
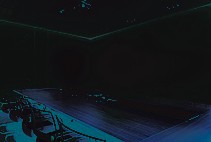
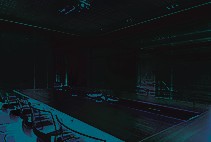
GTAW/ TIG welding
Gas tungsten arc welding (GTAW), also known as tungsten inert gas (TIG) welding, is an arc welding process that uses a nonconsumable tungsten electrode to produce the weld. The weld area is protected from atmospheric contamination by a shielding gas (usually an inert gas such as argon), and a filler metal is normally used, though some welds, known as autogenous welds, do not require it. A constant-current welding power supply produces energy which is conducted across the arc through a column of highly ionized gas and metal vapors known as a plasma.
SMAW/ MMA welding
Shielded metal arc welding (SMAW), also known as manual metal arc (MMA) welding or informally as stick welding, is a manual arc welding process that uses a consumable electrode coated in flux to lay the weld. An electric current, in the form of either alternating current or direct current from a welding power supply, is used to form an electric arc between the electrode and the metals to be joined. As the weld is laid, the flux coating of the electrode disintegrates, giving off vapors that serve as a shielding gas and providing a layer of slag, both of which protect the weld area from atmospheric contamination.
MIG/ MAG welding
Gas metal arc welding (GMAW), sometimes referred to by its subtypes metal inert gas (MIG) welding or metal active gas (MAG) welding, is a semi-automatic or automatic arc welding process in which a continuous and consumable wire electrode and a shielding gas are fed through a welding gun. A constant voltage, direct current power source is most commonly used with GMAW, but constant current systems, as well as alternating current, can be used. There are four primary methods of metal transfer in GMAW, called globular, short-circuiting, spray, and pulsed-spray, each of which has distinct properties and corresponding advantages and limitations.
Spot welding
Spot welding is a process in which contacting metal surfaces are joined by the heat obtained from resistance to electric current flow. Work-pieces are held together under pressure exerted by electrodes. Typically the sheets are in the 0.5-3.0 mm thickness range. The process uses two shaped copper alloy electrodes to concentrate welding current into a small 'spot' and to simultaneously clamp the sheets together. Forcing a large current through the spot will melt the metal and form the weld. The attractive feature of spot welding is a lot of energy can be delivered to the spot in a very short time (ten to one hundred milliseconds). That permits the welding to occur without excessive heating to the rest of the sheet.
During the 1920s, major advances were made in welding technology, including the 1920 introduction of automatic welding in which electrode wire was continuously fed. Shielding gas became a subject receiving much attention as scientists attempted to protect welds from the effects of oxygen and nitrogen in the atmosphere. Porosity and brittleness were the primary problems and the solutions that developed included the use of hydrogen, argon, and helium as welding atmospheres. During the following decade, further advances allowed for the welding of reactive metals such as aluminium and magnesium. This, in conjunction with developments in automatic welding, alternating current, and fluxes fed a major expansion of arc welding during the 1930s and then during World War II.
During the middle of the century, many new welding methods were invented. Submerged arc welding was invented in 1930 and continues to be popular today. Gas tungsten arc welding, after decades of development, was finally perfected in 1941 and gas metal arc welding followed in 1948, allowing for fast welding of non-ferrous materials but requiring expensive shielding gases. Using a consumable electrode and a carbon dioxide atmosphere as a shielding gas, it quickly became the most popular metal arc welding process. In 1957, the flux-cored arc welding process debuted in which the self-shielded wire electrode could be used with automatic equipment, resulting in greatly increased welding speeds. In that same year, plasma arc welding was invented. Electroslag welding was released in 1958 and was followed by its cousin, electrogas welding, in 1961.
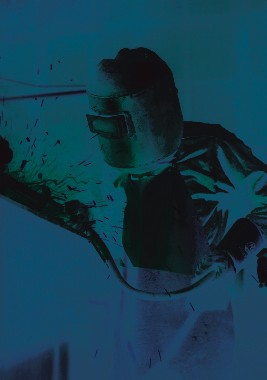
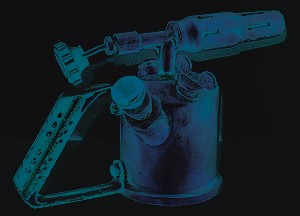
Welding accidents
It's one of the most regulated areas of the construction industry, but it's also one of the most dangerous. Welding accidents injure over 500,000 workers every year – and the injuries sustained due to a welding malfunction can lead to severe burns, even death.
Radiation
The arcs associated with arc welding emit high levels of ultraviolet radiation (UVR), and this often causes acute injuries in the workplace, particularly photokeratoconjunctivitis. It is important to know the level of UVR emitted by arc welding under various conditions, as this information will help in evaluating potential UVR hazards in welding workplaces and taking protective measures against it. The studies have shown that the ACGIH effective irradiance for UVR was measured experimentally for CO2 are welding in order to evaluate its UVR hazards. A welding robot was used in the experiment in order to realize reproducible and consistent welding operations.
The effective irradiance at 1 m from the arc was in the range 0.28–7.85 W/m2 (28–785 µW/cm2) under the study conditions. The corresponding permissible exposure time per day is only 4–100 s, suggesting that UVR from CO2 arc welding is actually hazardous for the eye and skin. It was found that the effective irradiance is inversely proportional to the square of the distance from the arc, is strongly dependent on the direction of emission from the arc with a maximum at 50–60° from the plate surface, and tends to increase with welding current.
Magnetic Field
Aim
To investigate cancer incidence in workers exposed to high levels of extremely low frequency magnetic fields (ELF-MF).
Methods
A cohort based on the engineering industry was established. Industries assumed to use resistance welding in production were chosen in order to increase the prevalence of high exposed subjects and to reduce the influence of confounding factors. All men and women employed in these branches during 1985–94 were selected: 537,692 men and 180,529 women. Occupation, based on census information from 1980, 1985, and 1990, was linked to a job exposure matrix on ELF-MF. Four exposure groups were used by stratifying on mean workday ELF-MF exposure, using the lowest exposure group as reference. Cancer incidence was obtained by linkage to the Swedish Cancer Registry.
Results
Men in the very high exposure group showed an increased incidence of tumours of the kidney, pituitary gland, and biliary passages and liver; for these cancer sites an exposure-response relation was indicated. Women in the very high exposure group showed an increased incidence of astrocytoma I–IV, with a clear exposure–response pattern. An association was suggested in the high exposure group only, for cancer of the corpus uteri and multiple myeloma. Decreased risks in the very high exposure group among men were found for cancer of the colon and connective tissue/muscle.
Conclusions
The results on cancer of the liver, kidney, and pituitary gland among men are in accordance with previous observations. Regarding brain tumours and leukaemia, the outcome for women provided further support of an association. The hypothesis of a biological mechanism involving the endocrine system was partly supported.
Smoke hazard
Welding entails risks that can be classified as risks deriving from physical agents (such as radiations, heat, electricity, noise) and risks linked to the inahalation of fumes, vapour and gases that are released during the welding process because of the high temperature.
A faulty insulation of the electric cables during the change of the electrodes can expose the worker to electrocution.
The heat coming from the smelted metallic material and the projection of incandescent particles may cause burns. Oxyacetylenic welding constantly entails a risk from infrared radiations, whereas electric-arc welding entails a risk both from infrared and ultraviolet radiations.
The decomposition of degreasing agents, lubricants and paint that are present on the pieces to weld can give origin to carbon monoxide, ammonia and phosgene.
Gases that are released during the welding process originate from acetylene's combustion, from the electrodes' coatings and from the modifications undergone by oxygen and nitrogen during the process. Nitrogen oxides and ozone are the determining factors in the respiratory risk of welders (welders' lung).
Nitrogen oxides originate from the oxidation of air nitrogen and the main one is nitrogen peroxide (NO2). Ozone originates from the action of ultraviolet rays on air oxygen.
Carbon monoxide formation is bigger in the MAG welding with CO2. Welding operations carried out in confined spaces without appropriate ventilation may entail a risk of acute intoxication from such gases. Welding fumes are made up of metallic vapour that is released in the smelting area; the presence of such fumes is bigger in the case of electric-arc welding. These fumes are mainly made up of iron and its oxides when welding involves ordinary steel, but they contain also big quantities of chrome, nickel and manganese in the case of special steel.
Powered air purifying respirator
This is a powered air respirator for welders. Speedglas welding shield with Adflo respirator is a light, compact, all-in-one system. Its exclusive 'stackable' configuration of the Adflo turbo unit means that the gas filter can be stacked onto the particle filter for additional protection from specific vapours.
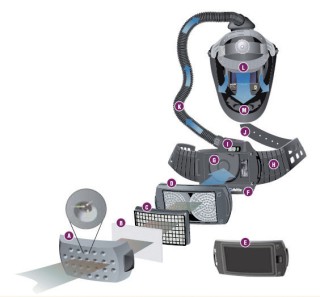
Hyperbaric welding
Hyperbaric welding is the process of welding at elevated pressures, normally underwater. Hyperbaric welding can either take place wet in the water itself or dry inside a specially constructed positive pressure enclosure and hence a dry environment.
It is predominantly referred to as 'hyperbaric welding' when used in a dry environment, and 'underwater welding' when in a wet environment. The applications of hyperbaric welding are diverse – it is often used to repair ships, offshore oil platforms, and pipelines. Steel is the most common material welded.
Dry hyperbaric welding is used in preference to wet underwater welding when high quality welds are required because of the increased control over conditions which can be exerted, such as through application of prior and post weld heat treatments. This improved environmental control leads directly to improved process performance and a generally much higher quality weld than a comparative wet weld. [...] Research into using dry hyperbaric welding at depths of up to 1,000 metres (3,300 ft) is ongoing. In general, assuring the integrity of underwater welds can be difficult (but is possible using various nondestructive testing applications), especially for wet underwater welds, because defects are difficult to detect if the defects are beneath the surface of the weld.
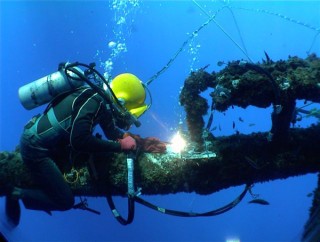
- en.wikipedia.org/wiki/Hyperbaric_welding
- http://amidac.com/yahoo_site_admin/assets/images/under_water_welding.140123929.jpg
Space welding
Welding in space is also possible – it was first attempted in 1969 by Russian cosmonauts, when they performed experiments to test shielded metal arc welding, plasma arc welding, and electron beam welding in a depressurized environment. Further testing of these methods was done in the following decades, and today researchers continue to develop methods for using other welding processes in space, such as laser beam welding, resistance welding, and friction welding. Advances in these areas may be useful for future endeavours similar to the construction of the International Space Station, which could rely on welding for joining in space the parts that were manufactured on Earth.
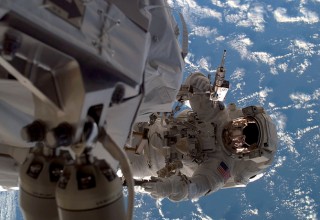