- Manufacturer: Issey Miyake Inc
- Designer: Issey Miyake & Dai Fujiwara
- Material: cotton
- www.isseymiyake.com
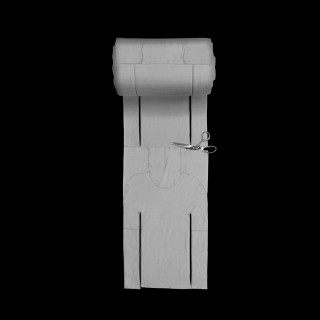
Index
- Issey Miyake Miyake was born 22 April 1938 in Hiroshima, Japan. As a seven year-old, he witnessed and survived the nuclear bomb dropped on Hiroshima on August 6, 1
- Dai Fujiwara Born in Japan in 1967, Dai Fujiwara is the textile engineer and designer at the Miyake Design Studio whose investigative work focuses on the possibili
- Weaving History The earliest form of fabric most likely came in the form of animal skins draped across the body for warmth, both as clothing and bedding. Because of t
- 3D Textiles A-POC refers to both the fashion label and the manufacturing process behind it. That process breaks one of the fundamental laws of fashion physics: cu
- 3D Textiles in Furniture APOC and Chairs Before the end of 2006, Miyake will offer consumers a product co-designed with London-based furniture maker/architect Ron Arad that bl
- APOC Stores Paris store by R & E Bouroullec 2000 The A-POC space in Paris was conceived of as a support: to carry the clothes and accessories of a collection that
- 21_21 DESIGN SIGHT Since the 1980s, Issey Miyake has delieved in the necessity of a design museum in Japan, and has discussed its importace with Isamu Noguchi, Ikko Tana
- Related Media Inventive Garments Designed to Go With the Flow Some dresses are flat, caftanlike silhouettes, corrugated with tiny pleats that can run vertically or,
- Cut Yourself Fashion Burda - cut yourself In 1949 Aenne Burda founded her own fashion printing and publishing company in the town of Offenburg, located in south-west Germa
Miyake was born 22 April 1938 in Hiroshima, Japan. As a seven year-old, he witnessed and survived the nuclear bomb dropped on Hiroshima on August 6, 1945. He studied graphic design at the Tama Art University in Tokyo, graduating in 1964. After graduation, he worked in Paris and New York City. Returning to Tokyo in 1970, he founded the Miyake Design Studio.
In the late '80s, he began to experiment with new methods of pleating that would allow both flexibility of movement for the wearer as well as ease of care and production. This eventually resulted in a new technique called garment pleating and in 1993's Pleats Please in which the garments are cut and sewn first, then sandwiched between layers of paper and fed into a heat press, where they are pleated. The fabric's 'memory' holds the pleats and when the garments are liberated from their paper cocoon, they are ready-to wear. He did the costume for Ballett Frankfurt with pleats in a piece named "the Loss of Small Detail" William Forsythe and also work on ballet "Garden in the setting".
He had a long friendship with Austrian-born pottery artist Dame Lucie Rie. She bequeathed to him her substantial collection of ceramic and porcelain buttons, which he integrated into his designs and presented them in new collections.
In 1994 and 1999, Miyake turned over the design of the men's and women's collections respectively, to his associate, Naoki Takizawa, so that he could return to research full-time. In 2007, Naoki Takizawa opened his own brand, supported by the Issey Miyake Group and was replaced, as a Creative Director of the House of Issey Miyake, by Dai Fujiwara.
Born in Japan in 1967, Dai Fujiwara is the textile engineer and designer at the Miyake Design Studio whose investigative work focuses on the possibilities of new technologies and fabrics. Dai Fujiwara joined the Miyake Design Studio in 1994 upon graduating from the Dyeing and Weaving Course at Tama Art University. After working as a member of the Issey Miyake Collection design staff, he launched the A-POC project with Issey Miyake in 1998.
The earliest form of fabric most likely came in the form of animal skins draped across the body for warmth, both as clothing and bedding. Because of their very composition, formed from protein and plant sources, early textiles tend to disintegrate over time, so there's very little evidence of their history. The best information we have about the history of fabric comes from the tools used in its creation.
In 1988, distinctive sewing needles made from bone were found near Russia. These needles were dated to around 18,000 B.C., and were likely used to sew animal skins together to form crude clothing. In addition, clay tablets have been found that show fabric weaving in the Middle East as early as 8,000 B.C. It's believed that the first hand looms were created around the same time.
The earliest surviving fabric scraps have been traced to Anatolia (near modern day Turkey, and can be dated to around 6,500 B.C. These include woven rugs, along with some scraps that indicate early wool cultivation. Fabric at this time was spun by hand or woven on primitive looms, and was formed from linen, wool and flax.
In China, silk production began around 2,800 B.C., and became a major export, opening up trade routes and partnerships with countries worldwide.
During the 1st century A.D., both cotton and wool production became popular, and more advanced looms were created to make weaving easier. It was also around this time that the first spinning wheel was created. The first evidence of knitted fabric is also traced to this period.
Through the Industrial Revolution of the 19th century, the majority of fabric production was done locally. Raw materials such as silk, lace or linen were traded among the wealthy, but the average person wore homespun or knitted wool and cotton garments. As steam and water-powered machinery became available in the 19th century, fabric production in Western Europe and North America shifted to centralized factories.
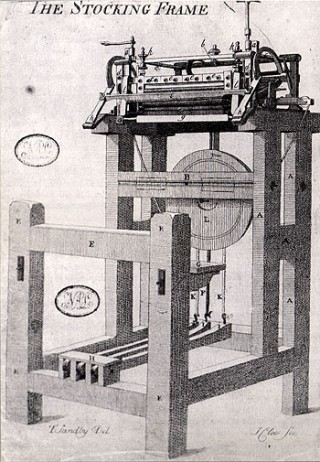
A-POC refers to both the fashion label and the manufacturing process behind it. That process breaks one of the fundamental laws of fashion physics: cut and sew. Normally, clothes are made by weaving thread or yarn into fabric, which is then snipped and stitched to create, say, a dress. The A-POC method requires no sewing. Thread goes into the loom, the dress comes out. Specifically, a flattened tube of material emerges that contains the finished shirt, skirt, or pants, which need only to be cut out along the faint outline already woven or knit into the fabric. Moreover, the material can be snipped anywhere without unraveling, a feature that allows for complete customization. A pair of scissors and a flirtatious spirit can turn a turtleneck into a plunging V-neck.
Miyake has so far kept the patent-pending process a closely guarded secret. But fashion insiders recognize that the technology behind A-POC - the process of melding thread into clothing, seamlessly - represents an entirely new way of making clothes, one that has less to do with the needles and bobbins of a garment factory than with rapid prototyping methods used in manufacturing. The real effect of A-POC has yet to be felt.
Textile manufacturing has a long history of sparking social and technological change. Joseph-Marie Jacquard's automatic loom, introduced in 1801, caused riots among the hand-weavers it began to displace, and later inspired Charles Babbage's Difference Engine and Herman Hollerith's punch cards. Likewise, the demise of cut-and-sew could have significant impact, allowing manufacturers to save time and money by eliminating work usually done by skilled laborers. "Miyake is weaving garments that don't need to be sewn," says Jack Lenor Larsen, an internationally renowned textile designer, "and that is the wave of the future."
But A-POC isn't just a new way to make clothes - it's a process that can be used to create all kinds of goods. Any material that can be turned into a fiber can work in the A-POC process, which gives Miyake the opportunity to produce anything from shoes to portable shelters. The A-POC team already has developed a series of colorful beanbag-like chairs and sofas that will come to market this year. The studio is also interested in a new corn-based fiber that could be used to construct other types of furniture, and it recently developed a resin-linen blend that a University of Tokyo lab found to be as strong as steel. To branch out, Miyake is looking into partnerships or licensing agreements.
Toshiko Mori, an architect and professor at the Harvard Graduate School of Design, sees A-POC as a prototype for the future of design and fabrication. "I think we can make houses and building components with this technique in a way that will be both economical and offer enormous design possibilities," she says. "It's a high tech, high design, low-cost solution."
Complete garment knitting
Complete garment knitting is a next-generation form of fully-fashioned knitting that adds the capability of making a 3-dimensional full garment. Unlike other fully-fashioned knitting, where the shaped pieces must still be sewn together, finished complete knitted garments do not have seams. The knitting machines' computerized instructions direct movement of hundreds of needles to construct and connect several tubular knitted forms to create a complete garment in a single production step.
The complete garment system's advantages lie in 1) a further reduction in materials beyond even fully-fashioned production by eliminating seam allowances and 2) faster time to market by eliminating the need for sewing any components. These factors increases cost-effectiveness (especially important when using high-performance materials such as aramids for composites). One might also argue that cutting down on wased by-product selvage makes complete garment better for the environment.
Two companies manufacture complete garment knitting machines: Shima Seiki and Stoll.
Examples of structures that are most often made with the complete garment technique are clothing (sportswear to sweaters) or technical textiles (car seat covers which also incorporate additional structural elements such as metal and plastic fasteners, composite preforms). The machines can produce a variety of topologies that were more difficult or impossible to create with knitting machines before, including: connected tubes, circles, open cuboids, and even spheres (for helmet shells and other preforms).
Complete garment knitting requires two needle beds for three-dimensional structures (such as clothing). As is the case with all fully-fashioned knitting, machines require individual single needle selection (through electronic control) and presser feet (to hold down formed loops).
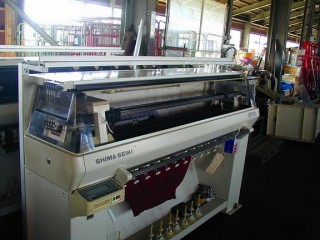
APOC and Chairs
Before the end of 2006, Miyake will offer consumers a product co-designed with London-based furniture maker/architect Ron Arad that blurs the edges between designer clothing and designer chairs. Called Gemini, it's a streamlined, body-cushioning seat pillow, made of A-POC fabric, which morphs into an elegant, body-hugging jacket. Arad points out that his curvaceous plastic Ripple chair, produced by Italian manufacturer Moroso, features what looks a lot like sculpted versions of Miyake's signature pleats.
"I did the Ripple chair, rather than do normal upholstery. And I have to say, when anyone does anything with ripples, it makes you think of Issey Miyake's work!" Arad says enthusiastically, the exclamation points palpable in his speech. "The design influence was there before we collaborated, so I thought, why not call A-POC? And what a go it was!"
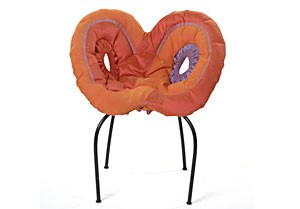
Other 3D knit furniture
Admittedly, Vitra has experience with 3D-textiles; at Orgatec this coming autumn, the company will be presenting a new office chair by the Bouroullecs that features a similar material. The fabric used for Slow Chair is unlike the 3D spacer fabrics that are currently making headlines and that are increasingly found in the mattress and car industries. In the furniture sector, spacer fabrics initially appeared as a covering for Patricia Urquiola's Lazy Lounge Chair for B&B Italia.
The knitting-machine program was altered endlessly, and countless fabric covers were made (a time-consuming operation, as the machine takes around two hours to produce one backrest cover), fitted experimentally and rejected before the optimum measurements were determined.
"Varying degrees of elasticity make for zones that differ in tautness and flexibility," says Maise. "However, the average thickness of the material is around two mm, which produces a chair with both the desired transparency and a sculptural look."
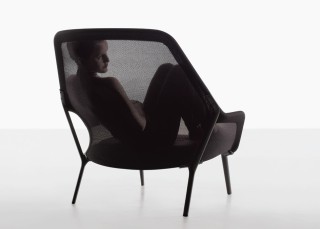
Paris store by R & E Bouroullec 2000
The A-POC space in Paris was conceived of as a support: to carry the clothes and accessories of a collection that changes and evolves every six months. The very open principle allows the space to have a different image over the course of time.
The framework is a Corian® structure that runs along the walls and the ceiling. It is composed of three horizontal bars, a traditional one at the height of a clothes rail, one higher and one lower. The ceiling is criss-crossed with bars that primarily serve to carry the clothes on hangers. The heads of the hangers are hidden at the back of the bar. Then, a series of accessories, which are also placed on the framework, allows you to arrange other elements in a different way: big vertical metal plaques act as boards to which the clothes have been attached with magnets; horizontal plates hold clothes laid out flat, and also shoes or bags. Finally a play of little coloured plaques enables a form of punctuatation for the whole arrangement, allowing a distinction between the different ranges.
The curtains of the changing rooms are made up of a set of upholstered strips. They make the space of the changing rooms gentler, almost sound-proofed.
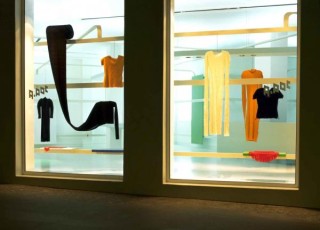
Aoyama, Tokyo store by Tokujin Yoshioka 2000.
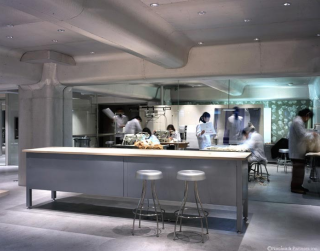
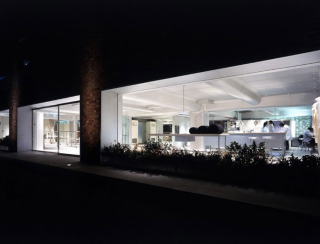
Since the 1980s, Issey Miyake has delieved in the necessity of a design museum in Japan, and has discussed its importace with Isamu Noguchi, Ikko Tanaka, Shiro Kuramata, Tadao Ando and other creators.
Following an article that he contributed to a newspaper in 2003, "Time to Create a Design Museum" , 21_21 DESIGN SIGHT opened in Tokyo Midtown on March 2007, with great support from Mitsui Fudosan Co., Ltd. and others.
21_21 DESIGN SIGHT was born as a venue to redirect our eyes to everyday things and events, and create various proposals and communicate numerous discoveries from the design point of view. As a place where visitors can be exposed to the pleasures of design and have new experiences filled with surprises, 21_21 DESIGN SIGHT focuses on exhibitions and runs a diversified program that includes talks and workshops. It is a launch pad that provides the vision (sight) to search for, discover, and make things indispensable to the times and design as culture that enlivens our daily lives.
To date, the venue has hosted exhibitions that take subjects close to us, like chocolate, water, man, nature, and bones, as their themes to turn our eyes toward society and make us think about the future.
Name
The name is read as "Two-one two-one design sight." It derives from the term in English for perfect vision, "20/20 Vision" (or sight), and was named to express our wish to become a venue that will generate design that sees even more clearly what is ahead. The logo is designed after the often-seen Japanese address number plates, which represents 21_21 DESIGH SIGHT's being a "place" of design, and the importance that design plays in everyday life.
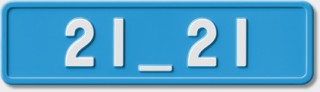
Directors
The directors are three designers who are well acquainted with the contemporary situation of design and the creative scene, Issey Miyake, Taku Satoh, and Naoto Fukasawa.
They are continually reviewing program planning with the associate director, Noriko Kawakami.
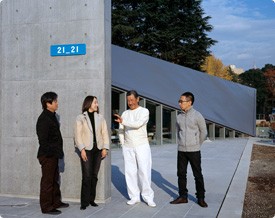
Inventive Garments Designed to Go With the Flow
Some dresses are flat, caftanlike silhouettes, corrugated with tiny pleats that can run vertically or, more loosely, in burnished horizontal waves; also flat is a gray jumpsuit, except that its pants legs are edged with ziggurat steps. Others are adamantly in the round, erupting with curves and billowing volumes that evoke flowers, leaves, Japanese armor or kimonos; when bounced, they roll up and down with the liquidity of Venetian blinds. Moving with Slinky-like jerks are several garments that are both pleated and wrinkled, including a layering of four flared tank tops, each longer and brighter than the last.
In a time of quotation and deconstruction, he has distinguished himself by being a staunch modernist, a sincere formalist you might say, who believes that new forms are possible and that they come out of a combination of historical consciousness and the deployment of new technology.
THE A-POC EPOCH
The garments are produced as enormous bolts of cloth, so that in a reversal of traditional fashion practice, in which designs are cut out and must then be sewn together, A-POC clothes are often fully made and then need only be cut out. In more recent collections, the sets must simply be separated from one another. In 1999, Fujiwara and another member of the A-POC team cut out the 'King and Queen' A-POC group in a live demonstration on the catwalk. The two of them quietly scissored out a succession of various skirt, top, trouser, and hood shapes on model Alex Wek's body before the audience's eyes.
Issey Miyake, the Dream Weaver
Never ones to stop pushing design to its most distant edges, Miyake and Fujiwara have been tinkering with the recipe for the fabric. "When we started A-POC we had no idea what its potential might be. It was a new way to make things using a new process. We have grown with the A-POC process," Miyake writes via e-mail from Japan. "Today, we feel that the potential for its applications can extend into many different areas of design. The challenge is to find materials that are suited to the process."
Fujiwara makes it clear that from the beginning of A-POC the creative duo was also simply looking for new ways to experiment with software programming. "Computer technology from the United States was a wave in the 1990s. And Issey is typhoon," says Fujiwara, who speaks in concise, nearly haiku-like sentences. "We wanted to make a new solution for making soft materials with computer technology. Hard materials have seen lots of new solutions."
Originally the prototypical A-POC fabric was a knit combination of wool, nylon, and polyurethane. In later incarnations, Miyake and Fujiwara created a more complex weave made of 100% cotton. The team later added elastic for flexibility, woven in layers to lend stretch.
Burda - cut yourself
In 1949 Aenne Burda founded her own fashion printing and publishing company in the town of Offenburg, located in south-west Germany. The first issue of her "burda fashion" magazine appeared in 1950. Ever-increasing magazine circulation confirmed her firm's success story because "burda fashion" soon became the world's best-selling magazine for home dressmakers! In 1987 "burda fashion" was the first western magazine to be published in the Soviet Union and in 1994 also the first western magazine to appear in the People's Republic of China.
Each monthly issue presents 50 new garments, many fashion and styling tips as well as a detachable supplement with the relevant comprehensive instructions and sewing pattern pieces.
Burda Pattern Collection
In 1952 Aenne Burda's publishing company began creating separate sewing patterns. Every January and July, it produces two sewing pattern catalogues with an assortment of over 600 styles for adults and children.
These practical individual sewing patterns contain precise and simple step-by-step instructions. They are designed at various levels of difficulty, from basic beginners to skilled seamstresses. Apart from standard clothing sizes, sewing patterns are also available for taller, petite and fuller figures (plus).
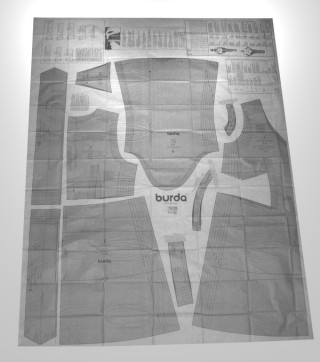
- www.schnittmuster-naehen.de/img/schnittmuster-beispiel.jpg
- www.burdafashion.com/en/All_about_burda/1000004-1033067.html
Muji freecut raincoat
Unique, made-to-measure unisex rainwear. Cut to desired length along the dotted line around the hem and sleeve cuffs of this E.V.A raincoat. Comes neatly folded in a pouch and is compact and easy to carry.
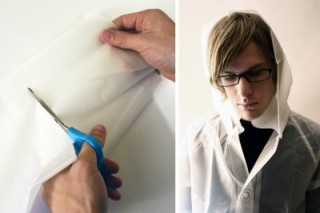